Co Injection Molding Services From China
Looking for a reliable Co Injection Molding partner? As a professional digital supplier, we can help. Get your plastic parts more easily and at a better price.
- 50+ Certified Materials & 15+ Surface Finishing Options
- Extensive Digital Manufacturing Expertise with a strong supply network
- Cost-effective solutions for both prototyping and mass production
- ISO 9001:2015 Certified, ensuring global quality standards
- High-precision Co Injection Molding with tolerances as tight as ±0.01 mm
Co Injection Molding Small Batch Production
At Formioo, we specialize in connecting you with high-precision Co Injection Molding services, providing cost-effective, reliable, and scalable manufacturing solutions for industries such as medical, electronics, automotive, and industrial equipment. Whether you need rapid prototyping or mass production, our trusted network of suppliers ensures that each part meets excellent precision and consistency.
With a trusted network of 200+ suppliers, we offer a wide range of Co Injection Molding capabilities, supporting everything from small-batch production to high-volume manufacturing. Our ISO 9001:2015-certified quality system ensures tight tolerances as precise as ±0.01 mm across a wide selection of 50+ materials and 15+ finishing options.
As one of the leading digital injection molding service providers in China, we are committed to providing cost-effective, high-performance parts with fast turnaround times. All of our custom-manufactured components are competitively priced without compromising on quality.
Our Co Injection Molding Services
Our partner Chinese factory specializes in Co Injection Molding technology, offering advanced techniques such as sequential, simultaneous, sandwich, and skin-core methods to produce multi-layer components. Utilizing state-of-the-art equipment and strict quality controls, we achieve high precision and reliable performance in both rapid prototyping and mass production. Our integrated digital manufacturing platform enables quick turnaround times, cost-effective production, and a range of customizable finishing options to meet diverse industrial needs.
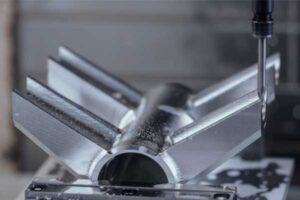
This method injects materials in a set sequence, creating distinct layers that optimize both surface aesthetics and core properties.
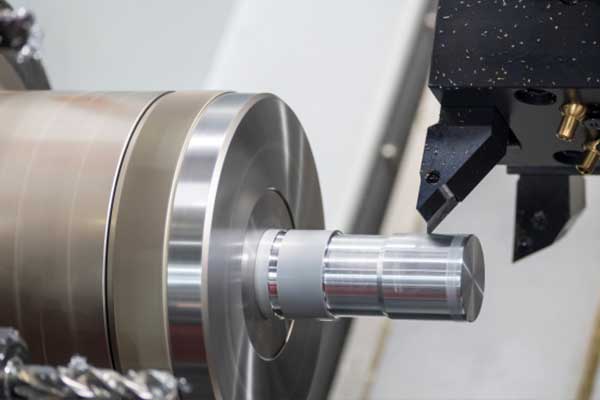
In simultaneous injection, multiple materials are fed concurrently, ensuring a homogeneous bond and seamless interface between layers.
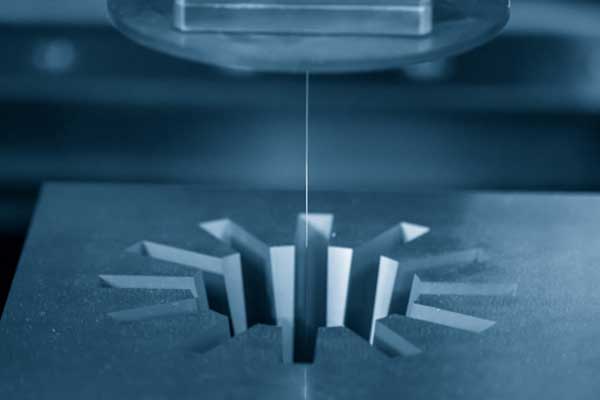
Sandwich molding layers a core material between two outer layers, enhancing impact resistance and structural rigidity in finished parts.
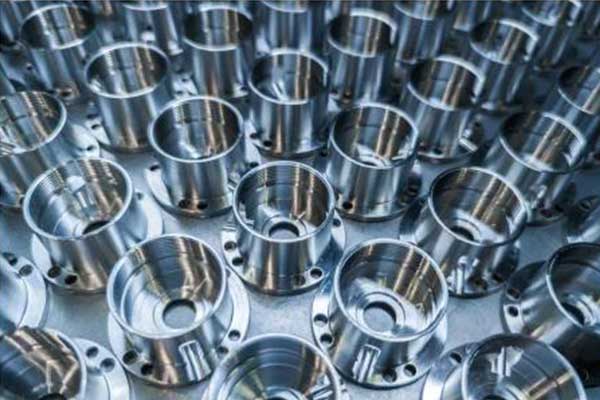
Skin-core molding forms a thin, high-quality outer skin around a cost-effective core, balancing aesthetics with functionality in components.
Co Injection Molding Capabilities
Material Compatibility
Our suppliers are capable of molding engineering plastics (POM, ABS, Nylon, PEEK, etc.), meeting various industrial and custom production needs.
Printing Accuracy
Our standard tolerance is controlled within ±0.01mm, ensuring high precision for medical, electronic, and industrial applications.
Maximum Build Size
Our maximum part size is up to 1000mm × 600mm × 500mm, suitable for small to medium-sized components.
Surface Finishing Options
We support polishing, sandblasting, powder coating, electroplating, laser engraving, and more for enhanced durability and aesthetics.
Delivery Time
Our standard Co Injection Molding lead time is 5-10 days, with expedited service available for urgent projects.
This is Modal Title
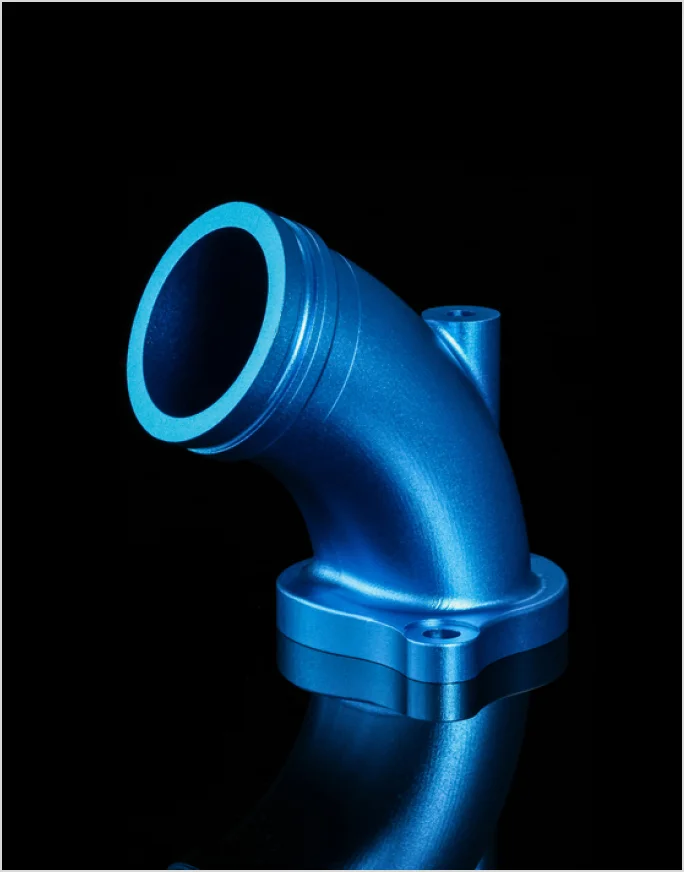
Our Latest Co Injection Molded Products We Have Manufactured
Explore our precision-engineered Co Injection Molded parts and see the quality for yourself. From prototyping to mass production, our high-precision components meet the toughest industry standards. Visit our website to view our finished products and discover how we can meet your manufacturing needs.
Co Injection Molding Materials
PP
Polypropylene (PP) is ideal for Co Injection Molding due to its low density, excellent chemical resistance, and superior melt flow properties. It can form strong, well-bonded layers, making it perfect for products that need a rigid outer shell with a softer core. In actual applications, PP is used to manufacture automotive interior panels, battery housings, and consumer packaging. For example, co-molded battery housings combine PP’s durability with lightweight performance, ensuring safety and longevity in daily use. Its versatility and cost-effectiveness make PP a frequent choice in high-volume production.
- Mill Lead Time: 2 days
- Color: Natural white with customizable tints
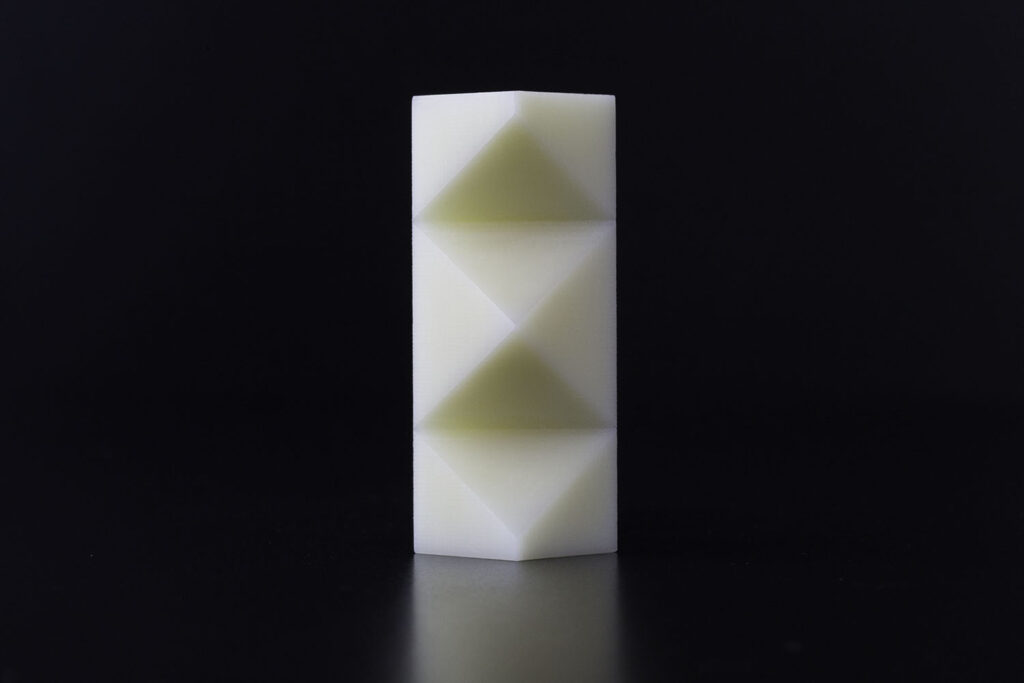
PE
Polyethylene (PE), including its high- and low-density variants, offers excellent processability and chemical stability for Co Injection Molding. Its smooth flow properties enable the creation of parts with a robust exterior and a flexible, energy-absorbing core. In practice, PE is widely applied in making fluid containers, piping systems, and protective housings. For instance, co-molded storage tanks benefit from PE’s moisture resistance and seamless layer bonding, enhancing durability even in harsh environments. Its low cost and high versatility make it suitable for both mass-produced and specialized components.
- Mill Lead Time: 3 days
- Color: Translucent base with a range of vibrant options
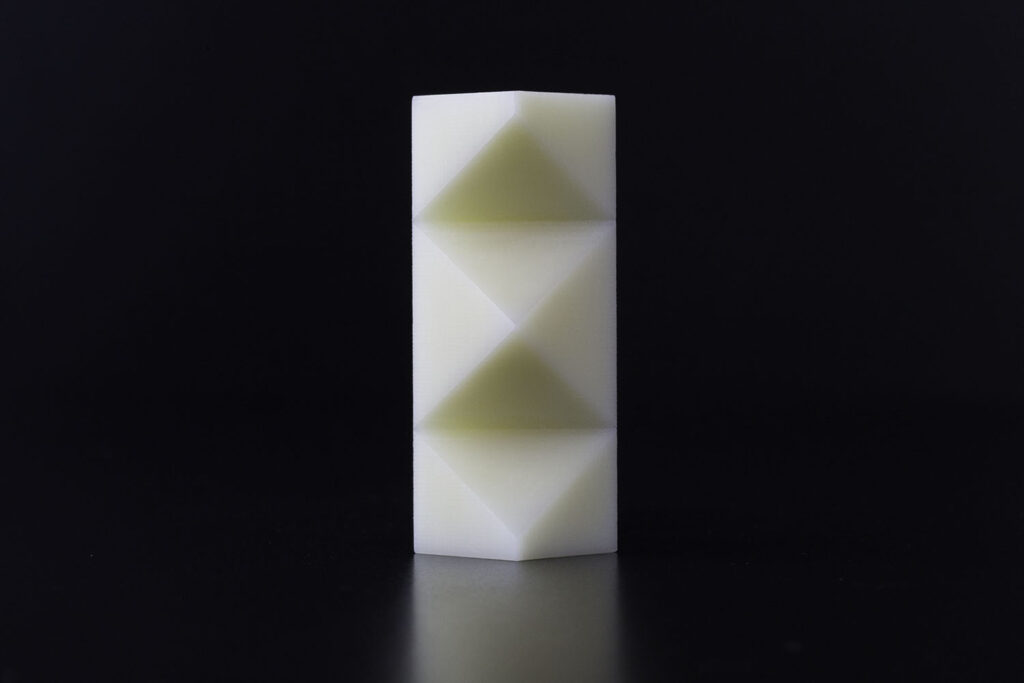
PS
Polystyrene (PS) is favored in Co Injection Molding for its ease of processing, dimensional stability, and ability to form clean interfaces between layers. Its rigid properties are balanced by a softer inner layer that improves impact resistance. In real-world applications, PS is used in consumer electronics housings, appliance panels, and decorative items. For example, co-molded electronic device casings utilize PS to achieve an attractive, glossy exterior with a cushioned interior that helps protect delicate components. Its cost-effectiveness and precision processing make PS an attractive option for both prototyping and production runs.
- Mill Lead Time: 2–3 days
- Color: Glossy clear or available in multiple colors
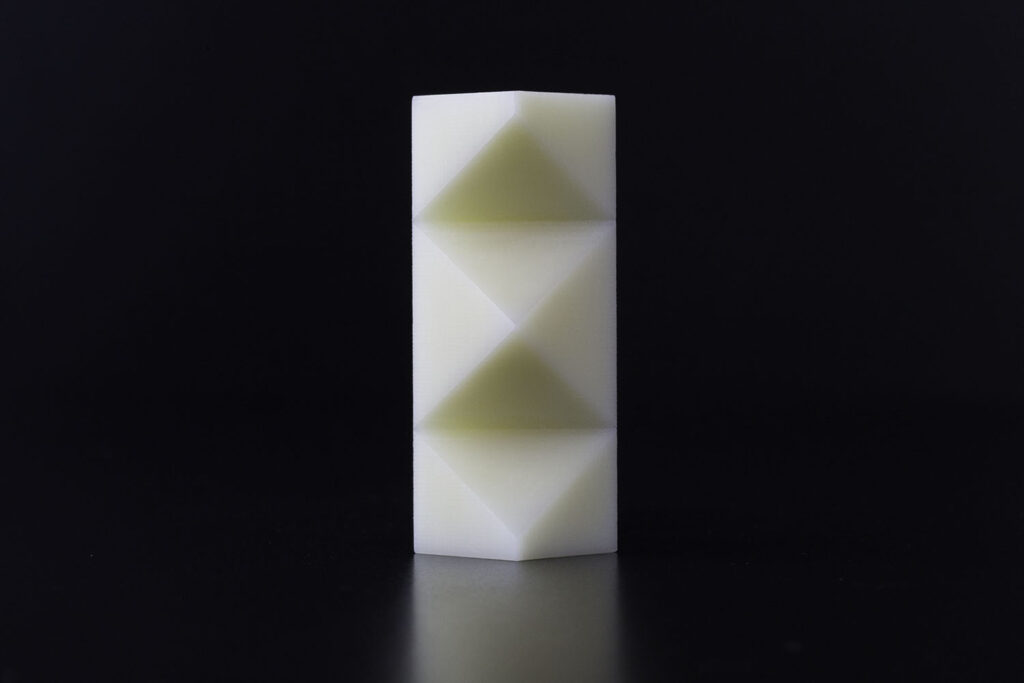
PVC
Polyvinyl Chloride (PVC) is well-suited for Co Injection Molding owing to its excellent weatherability, chemical resistance, and formulation flexibility. Its inherent toughness allows for a durable outer skin combined with a shock-absorbing inner layer. In actual applications, PVC is frequently used in window profiles, piping systems, and cable insulation. For instance, co-molded PVC components in construction benefit from enhanced impact resistance and longevity even under severe weather conditions. Its adaptability and performance consistency under varied conditions make PVC a reliable choice for both industrial and consumer products.
- Mill Lead Time: 3–4 days
- Color: Base white or gray with customizable finishes
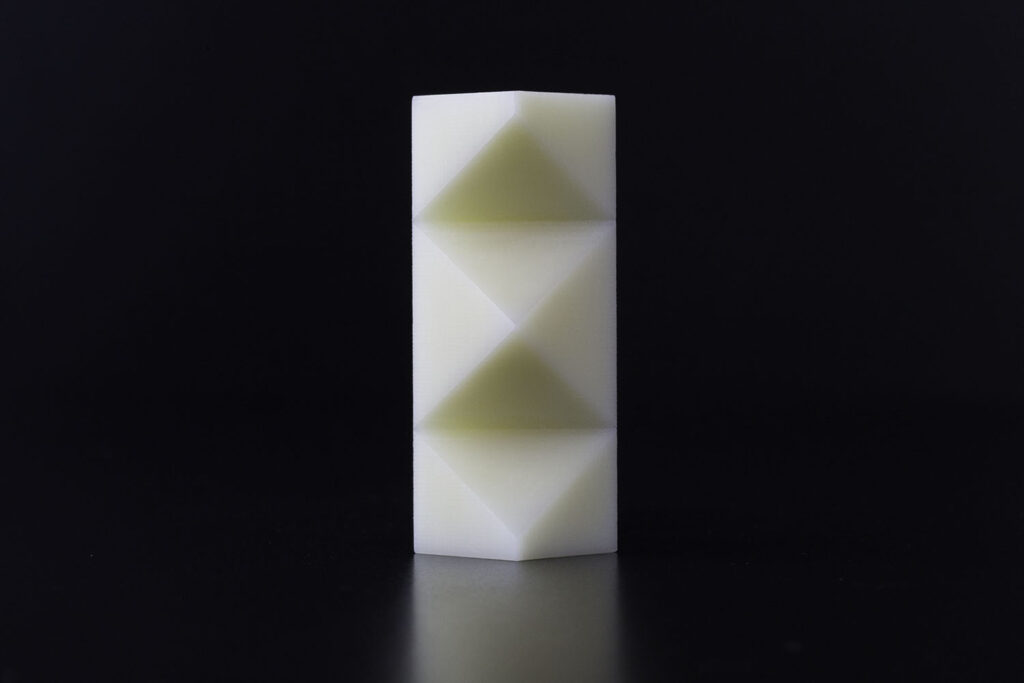
PC
Polycarbonate (PC) is highly regarded in Co Injection Molding for its exceptional impact strength, clarity, and thermal stability. Its properties allow for the production of parts with a transparent, scratch-resistant outer layer combined with a resilient, energy-absorbing core. In real-life applications, PC is used to create optical lenses, protective covers, and electronic device housings. For example, co-molded protective casings for consumer electronics exploit PC’s clarity and toughness, ensuring both aesthetic appeal and durability. This unique combination of attributes makes PC a go-to material for high-precision and high-reliability components.
- Mill Lead Time: 5 days
- Color: Transparent or tinted, with clear options available
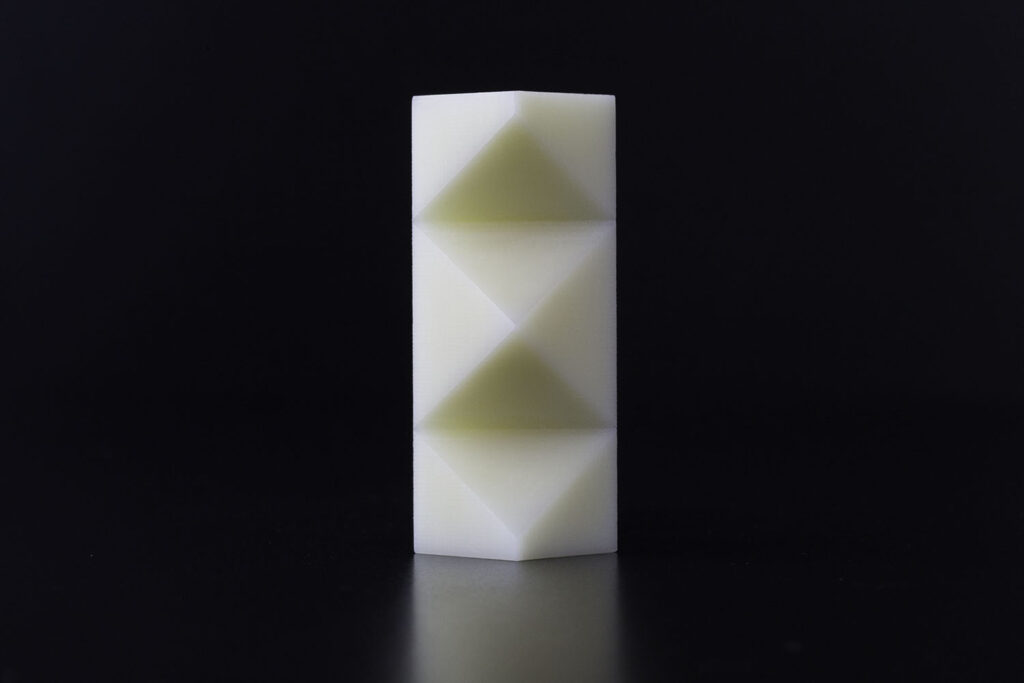
PA
Polyamide (PA), commonly known as Nylon, is favored in Co Injection Molding for its excellent mechanical strength, wear resistance, and toughness. Its ability to bond well with other materials makes it ideal for layered structures that require a robust outer skin with an energy-absorbing inner core. In actual applications, PA is employed in producing gears, fasteners, and structural components in the automotive and industrial sectors. For instance, co-molded fasteners exhibit enhanced durability and reduced friction, ensuring reliable performance in dynamic mechanical systems. Its flexibility in processing and superior endurance under load are significant advantages.
- Mill Lead Time: 4–5 days
- Color: Natural off-white to light brown tones
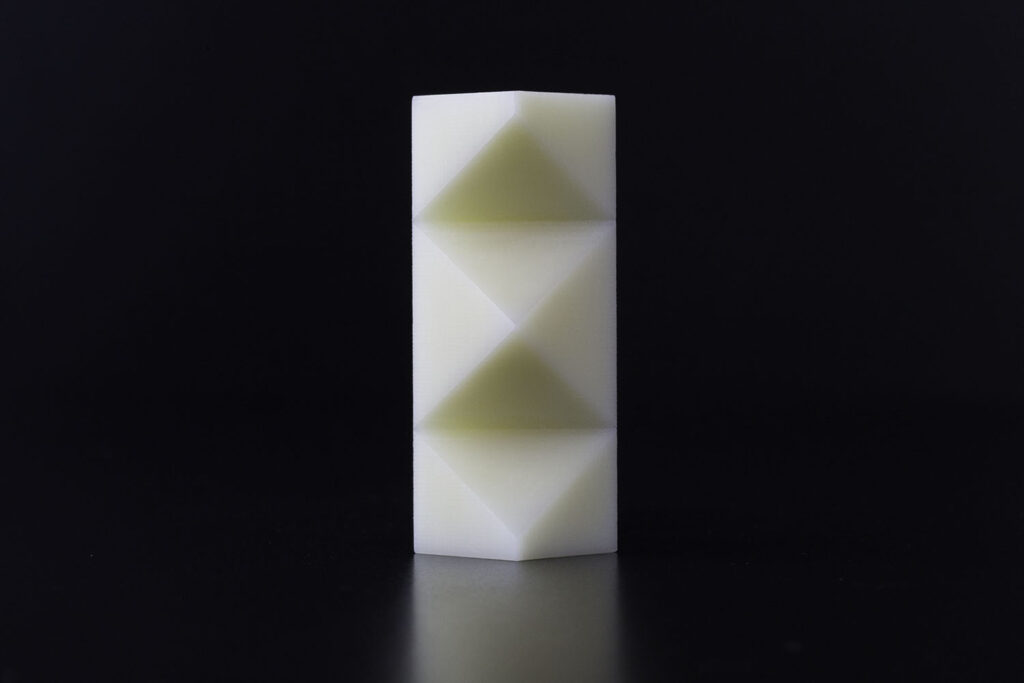
POM
Polyoxymethylene (POM) is chosen for Co Injection Molding due to its exceptional dimensional stability, low friction, and fatigue resistance. It enables the fabrication of parts featuring a rigid, high-strength outer layer with a softer core that absorbs impact. In practical use, POM is widely applied in the manufacture of precision gears, bearings, and other moving components. For example, co-molded POM parts in automotive transmissions benefit from enhanced accuracy and durability under cyclic loads. Its excellent machinability and long-term stability make POM a preferred choice in demanding engineering applications.
- Mill Lead Time: 5 days
- Color: Cream or off-white with natural appearance
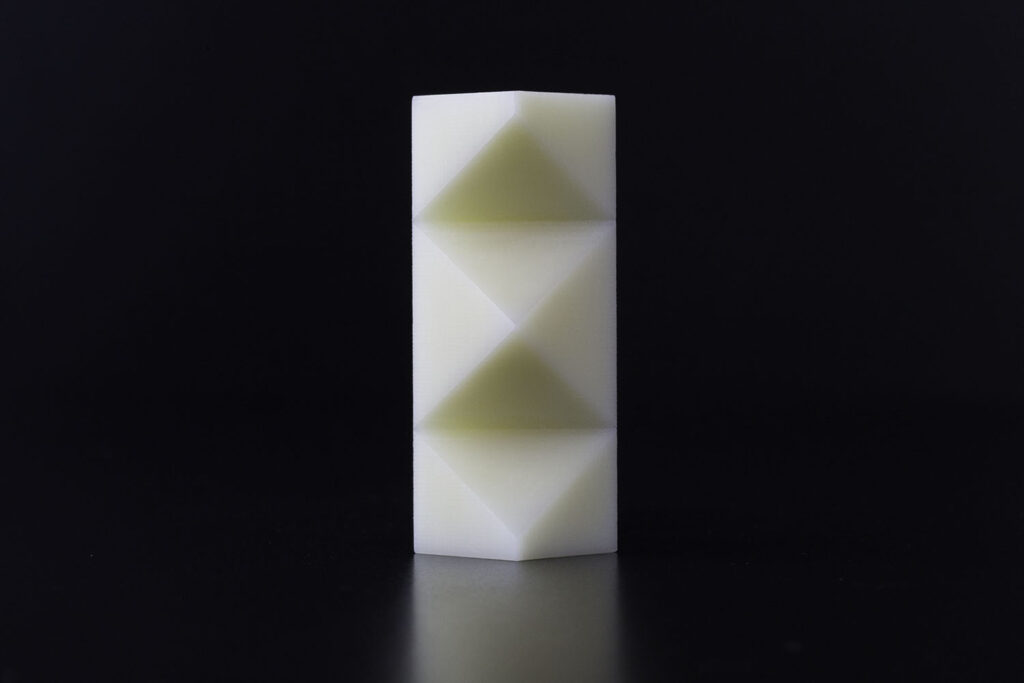
PEEK
PEEK is a top-tier material for Co Injection Molding in high-performance applications due to its exceptional thermal stability, chemical resistance, and mechanical strength. Its ability to be co-injected allows for parts with a hard, temperature-resistant outer layer and a more flexible inner core. In real-world scenarios, PEEK is used in aerospace components, medical devices, and high-stress industrial parts. For example, co-molded PEEK structures in aircraft components offer outstanding performance under extreme temperatures and loads, ensuring safety and longevity. Its high reliability in harsh environments makes it invaluable for critical applications.
- Mill Lead Time: 7–10 days
- Color: Natural amber or customizable shades
is a top-tier material for Co Injection Molding in high-performance applications due to its exceptional thermal stability, chemical resistance, and mechanical strength. Its ability to be co-injected allows for parts with a hard, temperature-resistant outer layer and a more flexible inner core. In real-world scenarios, PEEK is used in aerospace components, medical devices, and high-stress industrial parts. For example, co-molded PEEK structures in aircraft components offer outstanding performance under extreme temperatures and loads, ensuring safety and longevity. Its high reliability in harsh environments makes it invaluable for critical applications.
- Mill Lead Time: 7–10 days
- Color: Natural amber or customizable shades
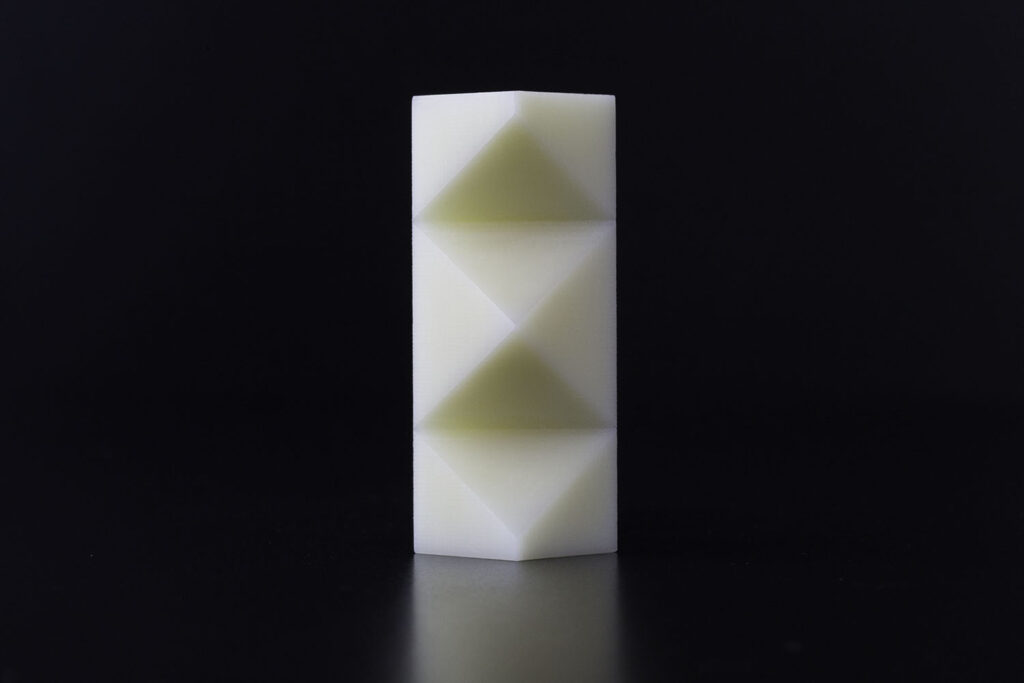
PPS
Polyphenylene Sulfide (PPS) is favored for Co Injection Molding in high-performance scenarios due to its outstanding thermal stability, chemical resistance, and dimensional precision. The co-injection process allows PPS to form parts with a hard, durable outer layer and a softer inner core that improves impact absorption. In practice, PPS is used in automotive under-hood components, electrical connectors, and industrial machinery parts. For example, co-molded PPS components in engine compartments deliver high reliability by withstanding extreme temperatures and chemical exposure, ensuring long-term performance. Its balance of toughness and precision is key to its application.
- Mill Lead Time: 6–8 days
- Color: Typically gray, with adjustable color formulations
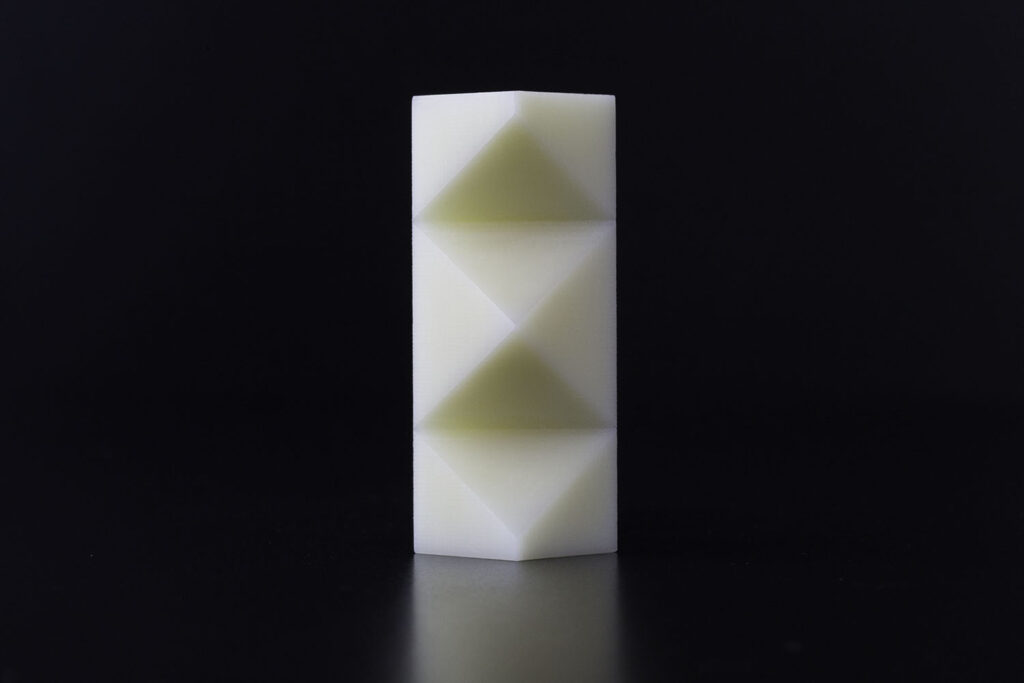
PI
Polyimide (PI) is an exceptional material for Co Injection Molding, celebrated for its high temperature endurance, excellent mechanical properties, and electrical insulation. Its use in co-molded parts results in a robust outer layer paired with a flexible inner layer that dampens impact. In practical applications, PI is widely used in aerospace, electronics, and industrial sectors, such as in high-performance circuit boards and thermal management components. For example, co-molded PI parts in aerospace systems deliver reliable operation under continuous thermal stress and vibration, ensuring the safety and efficiency of advanced technologies.
- Mill Lead Time: 8–10 days
- Color: Typically yellowish-brown, with potential for customization
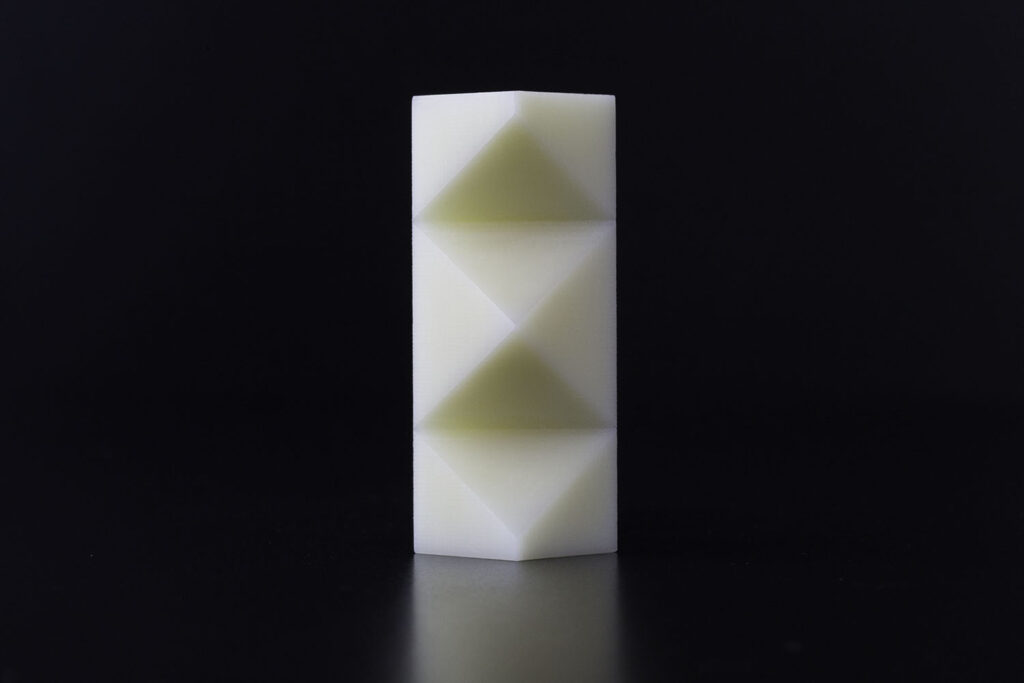
PEI
Polyetherimide (PEI) is highly suitable for Co Injection Molding because of its remarkable heat resistance, flame retardancy, and dimensional stability. Its properties support the production of parts with a high-performance, rigid exterior and an impact-resistant inner layer. In practical applications, PEI is commonly found in high-end electrical housings, aerospace components, and medical instruments. For instance, co-molded PEI parts in electronic devices ensure both fire safety and mechanical strength under demanding thermal conditions. Its excellent performance under heat and stress makes it a prime choice for premium, high-reliability products.
- Mill Lead Time: 7 days
- Color: Natural light brown with options for custom coloration
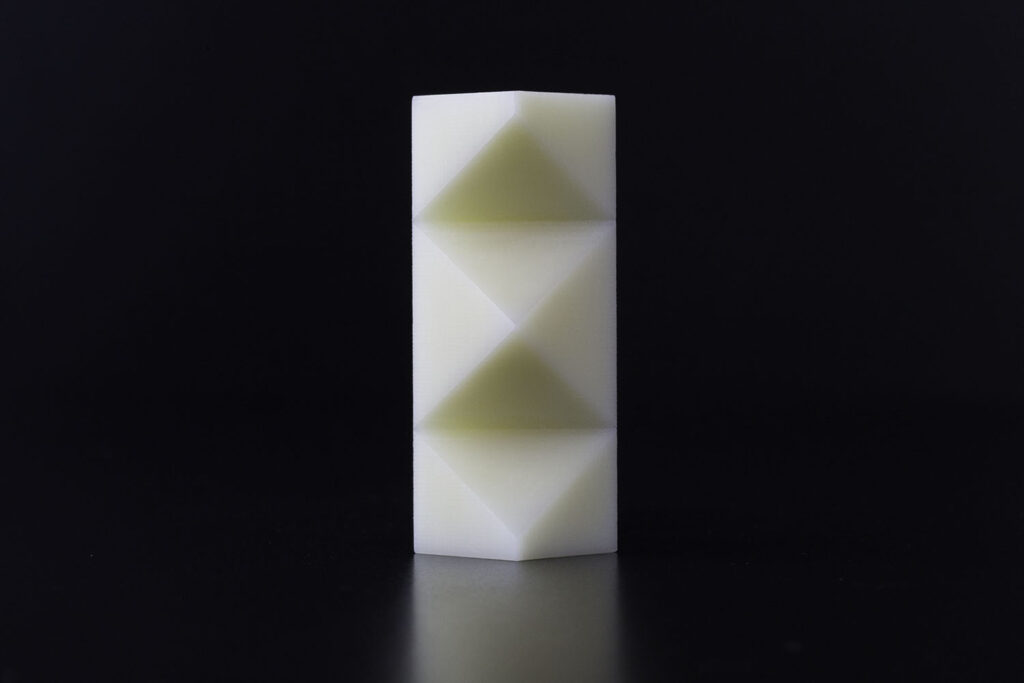
Finishing Options for Co Injection Molding
Name | Applicable Materials | Colors | Can Be Applied With |
---|---|---|---|
UV Coating | Co-injected plastics (PP, ABS, PC, etc.) | Clear, tinted | UV curing systems |
Spray Painting | Various plastics and metals | Wide color spectrum | Automated spray booths |
Pad Printing | Plastics (ABS, PC, PP, etc.) | Full color range | Custom pad printing machines |
Silk Screen Printing | Plastics and composites | Multi-layer, vibrant | Screen printing systems |
Laser Engraving | Laser-compatible plastics (ABS, PC) | Surface modification effects | Laser engraving systems |
Electroplating | Pre-treated plastics (for metal finish) | Metallic (chrome, nickel, gold, etc.) | Electroplating baths |
Polishing | Injection molded thermoplastics | Natural finish variations (gloss/matte) | Mechanical polishing equipment |
Texturing | Plastics (ABS, PC, etc.) | Texture-dependent (varied patterns) | Mold texturing techniques, laser texturing |
Hot Stamping | Heat-resistant plastics (ABS, PC) | Metallic, foil finishes | Hot stamping machines |
Metalizing | Suitable plastics (ABS, PC) | Metallic (silver, gold, bronze, etc.) | Vacuum metallization, sputtering systems |
- *Additional finishing options include chromic acid anodizing, cadmium plating, copper plating, titanium anodizing (blue anodizing), gold plating, silver plating, and more. For materials not listed here, please contact us directly.
Co Injection Molding FAQs
Yes! We can use a lower-cost core material while maintaining a high-quality outer surface.
Definitely. Our co-injection process allows precise color control for both layers.
MOQ varies, but we’re flexible. Let’s discuss your project specifics.
Typically 4-6 weeks, but we can expedite if needed.
Yes, our advanced technology guarantees uniform layer distribution.
Of course! Our engineers will optimize your design for co-injection molding.
Are You Looking for Co Injection Molding Manufacturers in China?
Contact us for design assistance, free quote, and expert advice today.
Your inquiry will be replied within 24 working hours, and we respect your privacy.